Light poles play an essential role in ensuring safety, security, and aesthetics across various environments—from highways to parks and industrial zones. To meet the growing demand for durable and efficient light poles, investing in a light pole production line offers a streamlined, cost-effective solution. This article provides a comprehensive guide to the working principles of light pole production lines, their features, and the reasons why incorporating this machinery can benefit your manufacturing process.
We’ll also cover customization options, industry standards, and how a well-designed production line enhances efficiency, reduces costs, and boosts product quality. With growing urbanization across the globe, now is the perfect time to upgrade or establish your light pole manufacturing capabilities.
Working Principle of the Light Pole Production Line
A light pole production line consists of several integrated machines working in unison to transform raw materials, such as steel or aluminum, into finished light poles. The process involves multiple stages, including cutting, forming, welding, coating, and surface treatment. Let’s explore these key stages:
1. Material Cutting and Shearing
The first step in light pole production uses a cut-to-length line to cut steel or aluminum sheets into precise dimensions. A steel plates diagonally shearing machine trims the material into tapered or cylindrical shapes, depending on design needs.
2. Bending and Forming
Next, the cut material enters a tube bending machine or tandem press brake, where it bends into the desired pole shape. These machines efficiently handle both cylindrical and tapered pole designs, adapting to various customer specifications.
3. Welding and Joint Formation
After bending, the material undergoes welding, forming a seamless, durable structure. The automatic welding production line precisely welds longitudinal or spiral joints, ensuring structural integrity and longevity.
4. Hole Drilling and Component Installation
Drilling machines then create holes in the pole to accommodate mounting lighting fixtures or other components like solar panels. This step ensures the poles are functional and ready for installation.
5. Surface Treatment and Coating
To protect the poles from environmental factors like corrosion, the production line applies a surface treatment. The electrostatic spraying line coats poles with materials such as galvanization, powder coating, or anodizing, ensuring long-term durability, even in harsh outdoor environments.
6. Final Assembly and Quality Control
In the final stage, operators assemble additional components such as lighting fixtures or control boxes. The poles then undergo stringent quality control checks to guarantee they meet industry standards before being shipped for installation.
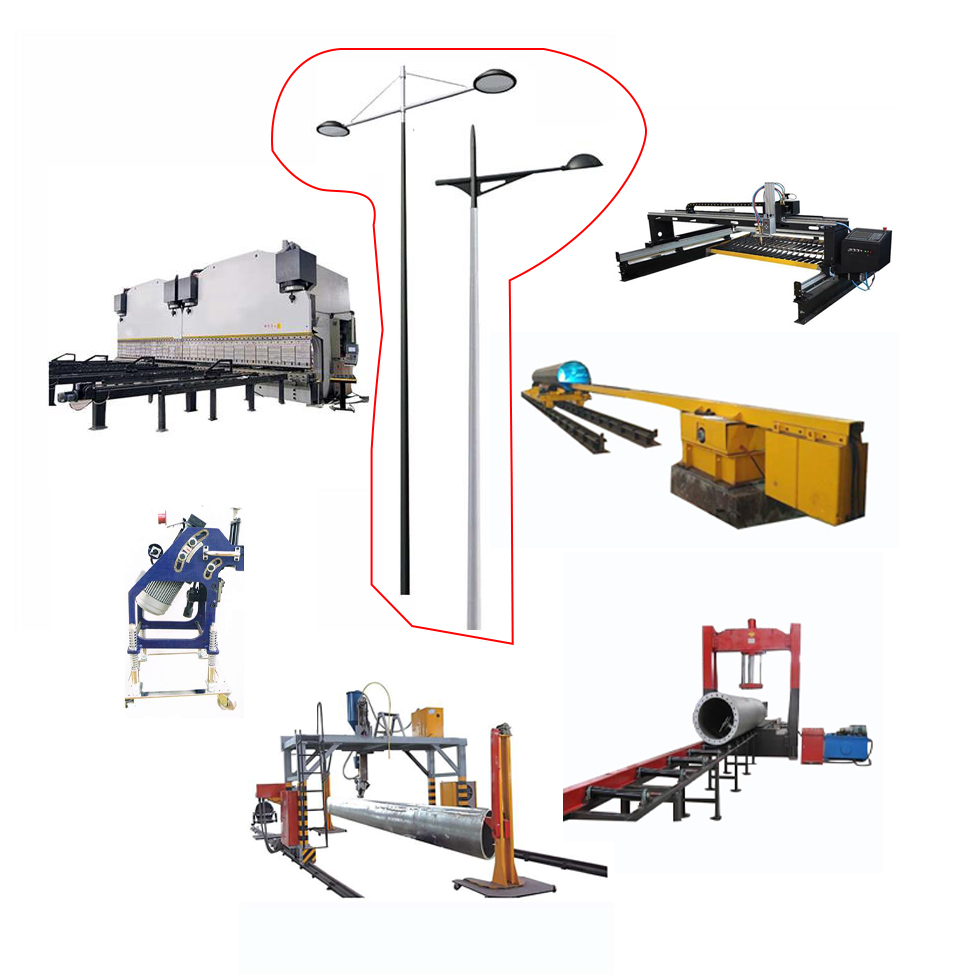
Key Features of the Light Pole Production Line
Investing in a light pole production line provides multiple features that improve both efficiency and product quality. Here are some key features that make this machinery a valuable asset:
1. Automation for Precision and Speed
Automation ensures each pole is manufactured to exact specifications. Tasks such as cutting, bending, welding, and surface treatment run with minimal error, increasing production speed and reducing waste.
2. Versatility in Materials
Our production line efficiently processes various materials like steel, aluminum, and fiber-reinforced plastic (FRP), catering to different market needs. This adaptability allows you to meet diverse customer demands.
3. Customizable Pole Designs
The system handles tapered, cylindrical, and custom pole designs. Switching between different designs is simple, thanks to the modular nature of the machinery.
4. Advanced Surface Treatment
The electrostatic spraying line offers multiple options, including galvanization, powder coating, and anodizing, which help the poles withstand harsh environmental conditions and extend their lifespan.
5. Energy Efficiency
Our line incorporates energy-efficient technologies, such as variable frequency drives (VFDs), which reduce electricity consumption without sacrificing production output.
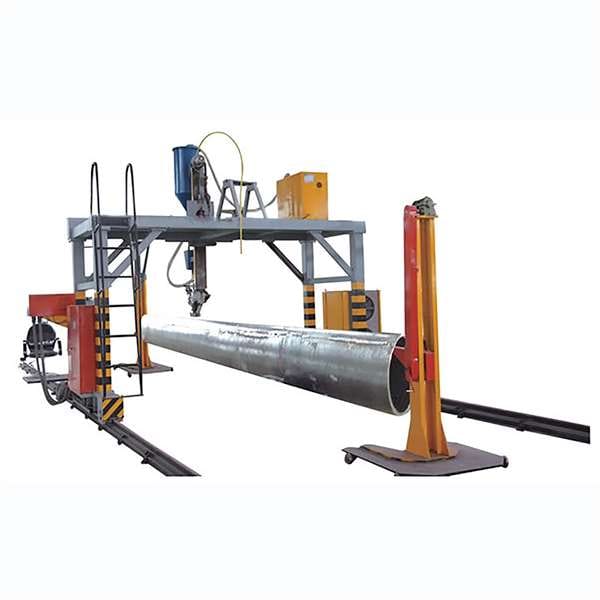
Why Choose a Light Pole Production Line?
Choosing a light pole production line provides multiple advantages for manufacturers looking to optimize efficiency and reduce costs. Below are several reasons why this investment is a smart choice for your business:
1. Increased Efficiency and Output
Automated processes make production faster and more precise, enabling your business to increase throughput. Tasks that previously relied on manual labor are now managed by high-tech machinery, ensuring greater efficiency.
2. Cost Savings
Automation reduces labor costs and minimizes waste. By optimizing the use of raw materials and reducing human errors, the line helps you achieve lower production costs while maintaining high product quality.
3. High-Quality Standards
The precision of automated welding, cutting, and coating processes ensures that each pole meets industry standards for strength, durability, and appearance, giving you a competitive edge in the market.
4. Customization for Market Demands
Whether for highway lighting or urban streetlights, the production line’s adaptability makes it easy to switch between different designs and materials. This versatility enhances your ability to serve various sectors.
5. Sustainability and Environmental Compliance
The growing focus on eco-friendly production requires businesses to adopt sustainable practices. Our production line supports this by using energy-efficient systems and allowing for the manufacturing of recyclable materials like aluminum.
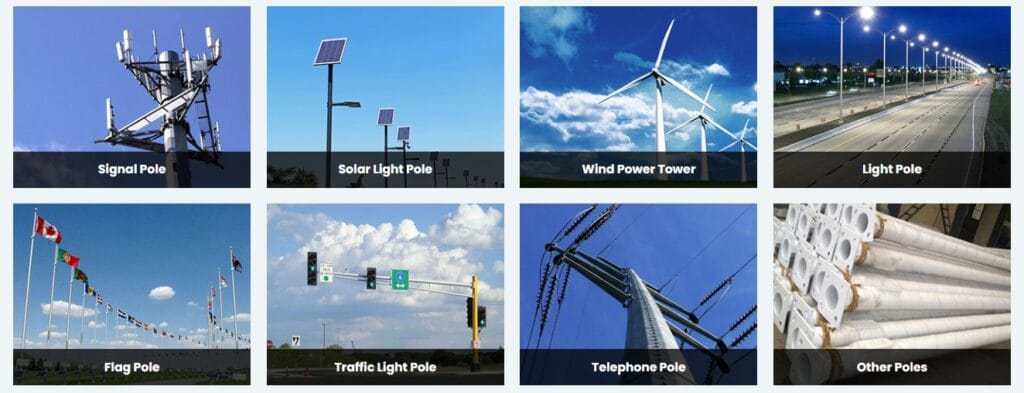
Industry Standards and Compliance
To ensure your light poles meet safety, quality, and environmental requirements, our production line adheres to stringent industry standards, which include:
1. Safety and Structural Integrity
Poles must endure exposure to elements like wind, rain, and impacts. Our line ensures that each pole meets required wind resistance and load-bearing standards, especially for high-traffic areas.
2. Corrosion Resistance
For poles installed in coastal or industrial areas, corrosion resistance is essential. Surface treatments like galvanization or anodizing protect poles from rust, enhancing their longevity.
3. Electromagnetic Compatibility (EMC)
Light poles in electromagnetic-sensitive areas, such as airports, must not interfere with nearby systems. The production line ensures that poles comply with EMC standards, providing a safe and interference-free installation.
4. Environmental Sustainability
With increasing attention to sustainability, the production line supports eco-friendly processes. The ability to work with recyclable materials and the energy-saving features help businesses align with modern environmental goals.
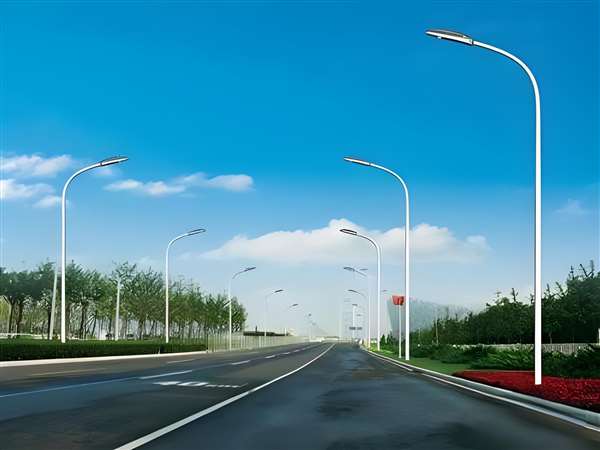
Customization Options for Light Pole Production
The light pole production line accommodates a wide range of customization options, allowing you to tailor the production process to specific project needs. Key options include:
1. Design Flexibility
The production line can produce poles in various shapes, including tapered and cylindrical designs. Whether you need standard or custom light poles, the machinery adjusts to different requirements.
2. Surface Coating Options
Coating customization ensures that poles withstand specific environmental conditions. Options such as galvanization, powder coating, and anodizing ensure optimal protection for different environments.
3. Integrated Features
With the rise of smart cities and sustainable energy solutions, light poles can integrate additional features like solar panel mounts or smart lighting systems. This capability ensures your products stay relevant in a growing market.
Enhancing Production Efficiency
Maximizing efficiency is crucial for staying competitive. Our production line includes several features that improve overall productivity:
1. Real-Time Monitoring
The production line includes IoT-based monitoring, allowing operators to track production status in real-time. This feature helps identify issues early and ensures seamless operations.
2. Quick Changeover
Quick changeover capability reduces downtime when switching between different pole designs or materials. This flexibility maximizes production output without sacrificing quality.
3. Energy Efficiency
The machinery incorporates advanced technologies designed to minimize energy consumption while maintaining high productivity, reducing both operational costs and environmental impact.
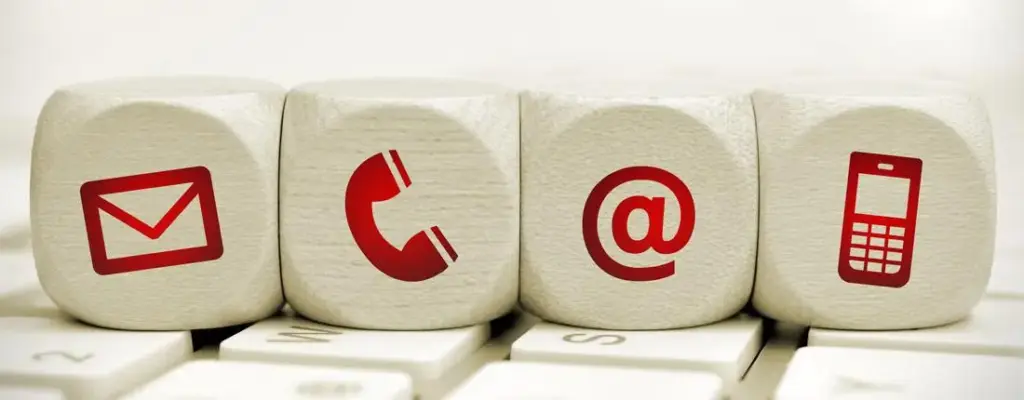
Take Action: Invest in the Future of Your Business
The demand for high-quality light poles continues to grow as urban areas expand and infrastructure projects rise. Our light pole production line allows you to meet these demands efficiently and effectively. Whether for highway lighting, urban developments, or park installations, this machinery enhances your production capabilities, enabling you to compete in a growing market.
By investing in this production line, you’re choosing a system that offers adaptability, cost savings, and sustainability. Ready to enhance your manufacturing process? Contact jiuying at liu@weldcnc.com or +008613394110095 to discuss how our light pole production line can transform your business.
Related Articles
- Auto beveling machine of light pole production line
- Light pole/power pole/communication tower pole production line
- Advanced Machinery: Efficiency in Light Pole Production
- Introducing Our Auto Beveling Machine for Light Pole Production Line
- Power Pole Production Line: How Are Metal Power Poles Made?
- Which Is the Most Popular Type of Light Pole in China?
- Introducing Our Auto Beveling Machine for Light Pole Production Line