At Jiuying, we recognize that street light poles play a crucial role in outdoor public spaces. Whether illuminating city streets, parks, or parking lots, these essential fixtures ensure safety and visibility in our daily travels. As demand for street light pole manufacturing continues to grow—due to new constructions and the need to replace aging infrastructure—understanding the intricacies of the manufacturing process becomes vital. In this blog, we will explore the various materials used, installation methods, components, and the step-by-step manufacturing process of street light poles.
Understanding Light Pole Materials
The type of material used for light poles greatly influences their applications, durability, and overall cost. Here’s a look at the most common materials:
Steel
Steel stands out as the most widely used material for street light poles due to its strength and durability. It withstands harsh weather conditions and supports multiple fixtures. However, it conducts electricity and is prone to rust and corrosion, which we must consider during installation.
Aluminum
Aluminum light poles offer a lightweight yet robust option. They resist corrosion, making them ideal for coastal areas. With a lifespan of over 50 years, aluminum poles require fewer replacements, providing a cost-effective choice in the long run. However, customers should note that they tend to be more expensive upfront compared to steel.
Fiberglass
Fiberglass poles strike a balance between strength and lightweight design. They are non-conductive and resistant to corrosion, rust, and vibrations. Typically lasting 20 to 30 years, fiberglass poles present a more expensive option than both steel and aluminum.
Wood and Concrete
While wood and concrete poles are also used, this blog will primarily focus on steel, aluminum, and fiberglass, as they remain the most common in modern applications.

Light Pole Installation Methods
We can categorize light pole installations into two types: direct burial and anchor-based systems.
Direct Burial Installation
In direct burial installations, workers embed poles directly into the ground without requiring a concrete base. This method simplifies installation and reduces costs, especially for aluminum and fiberglass poles that resist corrosion. However, this installation method may not suit loose soil and can complicate future pole replacements.
Anchor-Based Installation
Anchor-based installations involve securing the pole to a concrete footing using anchor bolts. While this method incurs higher costs and requires more time for installation, it offers easier replacements and greater stability against impacts.

Key Components of Light Poles
Before delving into the manufacturing process, it’s essential to understand the various components of light poles:
- Handhole/Cover: This access point allows electricians to reach internal wiring and comes with a tamper-proof cover.
- Conduit Hole: Located at the base, this hole facilitates the running of electrical wiring.
- Base Covers and Plates: These components enhance safety and aesthetics by covering visible bolts and improving the pole’s appearance.
- Pole Caps: Used to protect the top of the pole from rain and debris, they help prevent condensation issues.
- Anchor Bolts, Nuts, and Washers: Critical for securing anchor-based poles, these components ensure stability in various environmental conditions.
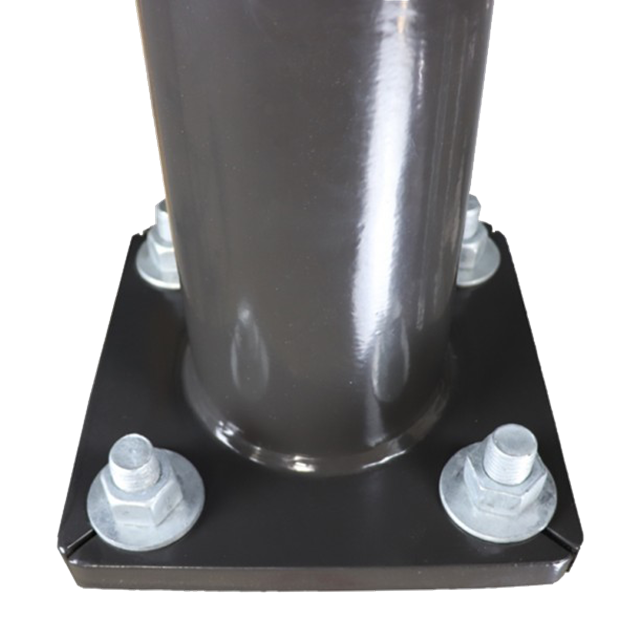
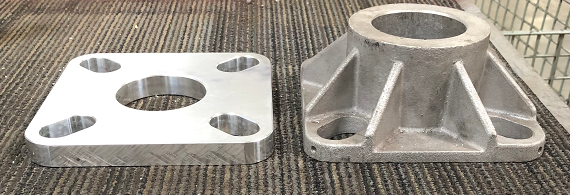

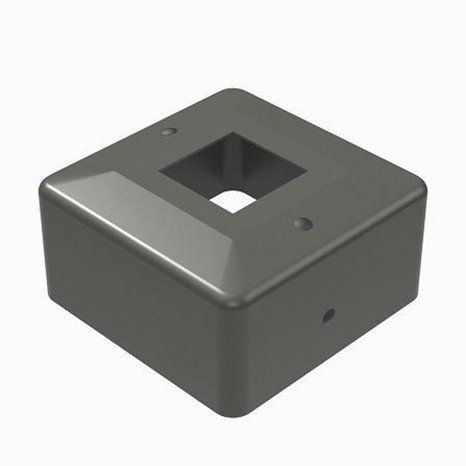
The Light Pole Manufacturing Process
The manufacturing process varies depending on the material used. Below is a general overview for each type:
Steel Pole Manufacturing
- Cutting: Manufacturers cut a flat steel sheet to the desired dimensions.
- Forming: The steel forms into a tubular shape through cold rolling or pressing.
- Cutting Holes: Technicians cut hand holes and mounting holes using laser or plasma technology.
- Welding: Workers attach the base plate through welding.
- Finishing: The pole undergoes painting, powder-coating, or galvanizing to prevent corrosion.
Aluminum Pole Manufacturing
- Molten Aluminum: Workers melt aluminum and pour it into molds to create the pole shape.
- Base Plate Attachment: They weld the base plate at the top and bottom of the pole.
- Cutting Holes: They then cut hand holes and mounting holes.
- Finishing Options: Poles can be anodized for a protective finish or powder-coated for durability.
Fiberglass Pole Manufacturing
- Cord Production: Manufacturers wind fiberglass strands together to create strong cords, which they dip in resin.
- Mandrel Shaping: The cords wrap around a spinning mandrel to form the pole shape.
- Curing: Steam is applied to cure the resin, solidifying the structure.
- Finishing: Workers sand the pole, cut necessary holes, and apply a protective coating.
Finishes and Treatments
Once manufacturers complete production, they can enhance durability with additional finishes:
- Powder Coating: This process applies a dry powder finish electrostatically, creating a hard, long-lasting surface.
- Galvanizing: Workers dip the pole into a zinc solution, which coats the pole to prevent corrosion.
- Anodizing: This electrolytic process applies a protective layer to aluminum poles, enhancing corrosion resistance.
Jiuying’s Commitment to Quality
At Jiuying, we take pride in our in-house manufacturing capabilities. This approach allows us to maintain high-quality standards throughout the production process. As a result, we can deliver superior products that meet the diverse needs of our customers in a timely manner.
If you’re interested in learning more about our street light pole manufacturing or wish to discuss a project, please feel free to reach out. Together, we can illuminate your outdoor spaces with quality and reliability.
Contact Us Today:
Email: liu@weldcnc.com
Phone: +86-13394110095
Send your inquiry now and explore how our advanced production line can meet your needs!
Related Articles
- Auto beveling machine of light pole production line
- Light pole/power pole/communication tower pole production line
- Advanced Machinery: Efficiency in Light Pole Production
- High-Efficiency Lighting Street Light Pole Production Line
- Street Light Pole Production Line: The Ultimate Solution for Modern Infrastructure
- Efficient Light Pole Production Line: Enhance Quality and Boost Productivity
- Power Pole Production Line: How Are Metal Power Poles Made?